Dopo aver terminato la costruzione del riflettore Dall Kirkham 310/6000 mi sono trovato di fronte a un dilemma. Era giunto il momento di scegliere, tra due contrapposte soluzioni, se acquistare o realizzare una montatura equatoriale alla tedesca idonea a sostenere il tubo ottico.
In quel periodo le montature equatoriali commerciali avevano una portata massima di 25 chilogrammi, mentre quelle più consone a sostenere il Dall Kirkham, con portata di almeno 50 chilogrammi, raggiungevano costi stratosferici.
L’autocostruzione della montatura, sebbene io stesso sia un forte sostenitore di questa pratica, non mi aveva per niente entusiasmato, perché troppo dispendiosa in termini di tempo e per l’incognita di trovarsi in seria difficoltà durante il corso della lavorazione. La scelta che facciamo in questi casi, la decisione di preferire una strada anziché l’altra, influenzerà immancabilmente il nostro futuro. Che fare?
Non sapendo che pesci prendere ho gestito il Dall Kirkham, per circa due anni, sulla montatura del rifrattore apocromatico alternando di tanto in tanto i due strumenti, un’operazione per niente agevole viste le notevoli dimensioni di entrambi.
Ad un certo punto, stanco di questa situazione e dopo una attenta valutazione dei costi, tenuto conto anche dell’elettronica da interfacciare, ho preso la decisione di realizzare una montatura equatoriale alla tedesca con tutti i rischi che ne avrebbero conseguito.
Per realizzare la montatura è indispensabile avere nella propria officina di casa un tornio parallelo e una fresatrice, altrimenti, avere un rapporto di amicizia e stima reciproca con un amico artigiano che sarà per buona parte l’esecutore materiale del progetto.
Per ottenere un ottimo risultato, sia da un punto di vista estetico che della precisione meccanica, è essenziale che nell’esecuzione dei vari componenti si rispetti sempre la massima accuratezza, e la meticolosità con cui si realizzerà un semplice foro o un accoppiamento foro-albero in tolleranza H7/h6 resterà di competenza dell’autocostruttore.
Il peggior nemico è la fretta. Al contrario, la perseveranza e la tenacia sono imprescindibili per riuscire a superare le difficoltà che si incontrano nel corso della realizzazione pratica e per risolvere quei problemi che si potrebbero presentare in modo del tutto imprevedibile, tra i quali la conseguenza di dover modificare il progetto in corso d’opera.
In questa lunga recensione che seguirà voglio presentare una dettagliata descrizione, integrata con foto e disegni tecnici, della montatura equatoriale alla tedesca che ho realizzato nel 2011.
A distanza di dieci anni ho deciso di apportare alcune modifiche interessanti per aumentarne le prestazioni e abbellirne l’estetica. Da qui se ne deduce, che una delle caratteristiche che principalmente distinguono l’autocostruzione è la possibilità di intervenire per ogni eventuale modifica che si volesse apporre.
La montatura può piacere o meno, avrà dei pregi e dei difetti costruttivi, ma quel che conta è la non lieve soddisfazione di essere riusciti a realizzare una montatura equatoriale alla tedesca solida e precisa.
La regolazione in Azimut e Latitudine
La base della montatura è formata da due flange accoppiate realizzate in alluminio Anticorodal 6082. Hanno rispettivamente un diametro di 274 mm e sono spesse 20 mm. La flangia di riscontro alla colonna portante del carrello ha un foro centrale di 50 mm di diametro realizzato in tolleranza H7 e due sedi necessarie per alloggiare due gabbie assiali a rullini SKF della serie AXK, rispettivamente AXK 50/70 e AXK 160/200.
La flangia mobile ha un mozzo di 50 mm di diametro, realizzato in tolleranza g6, con foro centrare di 30 mm. Ha inoltre due asole contrapposte di 30 mm di lunghezza e due sedi intermedie con madrevite che, per mezzo di due volantini con vite M10, mi consentono di ruotare la flangia in azimut di +/- 10°.
Le due flange vengono unite tramite l’accoppiamento foro-albero di 50 mm di diametro in tolleranza H7/g6, e consolidate dal precarico delle gabbie assiali a rullini AXK 50/70 e AXK 160/200. Il precarico è conseguito per mezzo di un bullone M30X3,5 (in ambito meccanico il termine bullone identifica l’accoppiata di vite e dado). Quest’ultimo, integrato con una gabbia assiale a rullini AXK 30/47, viene bloccato in dado contro-vite, ossia un dado avvitato contro una vite per impedirne l’allentamento.
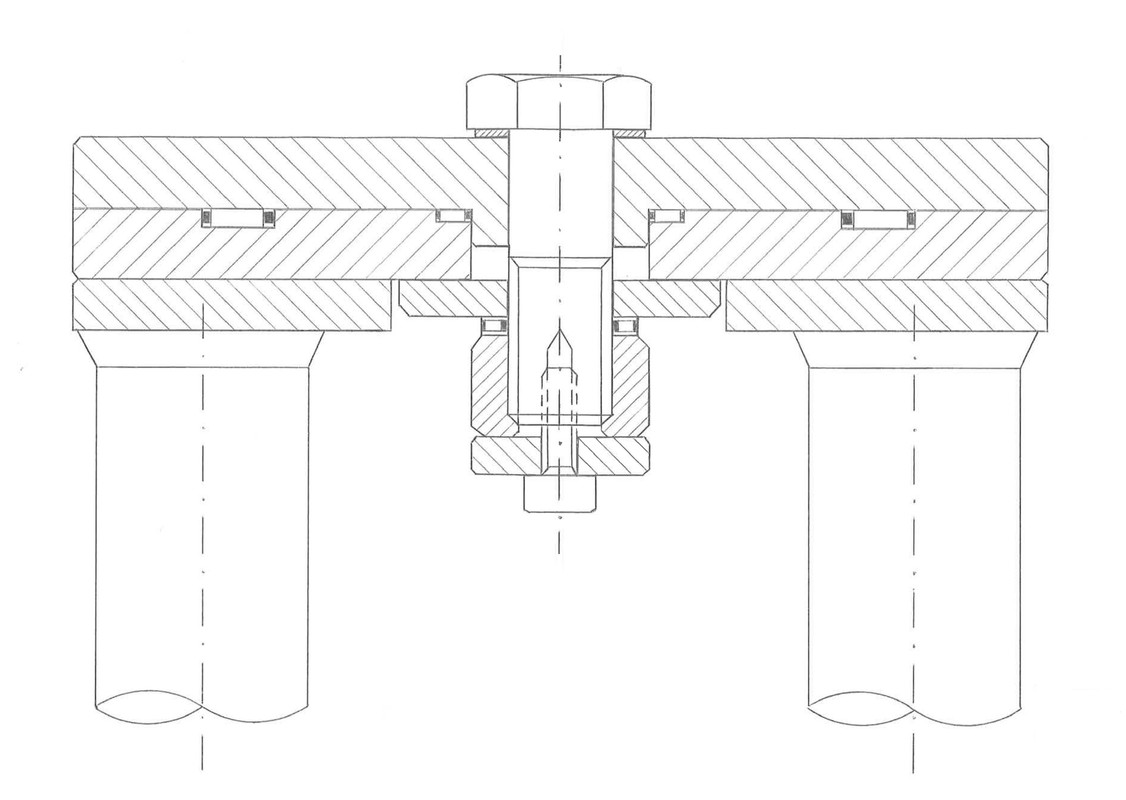
Rappresentazione a disegno degli elementi meccanici che consentono la regolazione in Azimut
Ne consegue, che il movimento della flangia mobile in azimut avviene per mezzo delle gabbie assiali a rullini AXK 50/70 e AXK 160/200, e non tramite lo strofinamento delle superfici a contatto delle due flange, come avviene in quasi tutte le montature equatoriali alla tedesca. Il precarico delle gabbie assiali a rullini mi permette di eseguire l’allineamento in azimut senza allentare il bullone centrale di blocco. In questo modo la base della montatura non viene soggetta a oscillazioni o a dislocamenti, che sono deleteri al fine di conseguire un perfetto allineamento.
In fase di realizzazione, l’assemblaggio meccanico delle due flange presenta un’insidia, poiché allineare sullo stesso piano le due gabbie assiali a rullini è un’operazione alquanto complessa. In questa circostanza, ho realizzato la sede della gabbia assiale centrale leggermente in sovrametallo, e dopo avere eseguito l’anodizzazione, ho riposizionato la flangia sul mandrino autocentrante del tornio e ho asportato il metallo in eccesso (pochi centesimi), verificando l’allineamento delle due gabbie assiali con una parallela in acciaio rettificata di precisione.
I due montanti che sostengono l’asse orario sono stati realizzati in alluminio Anticorodal 6082. Hanno rispettivamente uno spessore di 20 mm e sostengono l’asse orario tramite due perni in acciaio C40 di 20 mm di diametro integrati sul medesimo. I perni sono bloccati assialmente ad una estremità con testa a spallamento, all’altra con due volantini con madrevite M12.
La regolazione fine della latitudine (40° – 50°) è conseguita per mezzo di un congegno meccanico, realizzato in alluminio Anticorodal 6082, formato da un albero che viene inserito tra i due montanti e un’asta di manovra con vite M12. L’albero, con madrevite trasversale M12 al centro, è inserito tra i montanti in precarico e può ruotare su due boccole flangiate a riscontro frontale con accoppiamento H7/h6. La vite M12 viene azionata con una impugnatura e asta di manovra disposta a <T>.
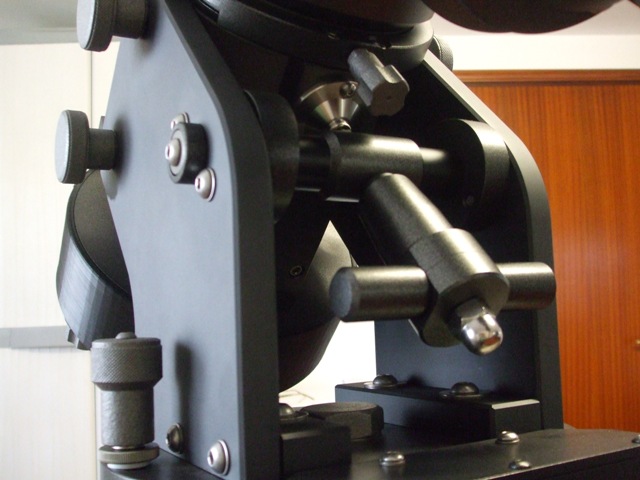
Il congegno meccanico che mi permette la regolazione fine della Latitudine
I due volantini posteriori svolgono il compito di serrare o allentare l’accoppiamento perno – boccola e consentire così la rotazione dell’asse orario, mentre quelli anteriori, quando viene ripristinato il serraggio, rendono il tutto come un unico corpo che scarica le forze sull’ampia superficie d’appoggio dei due montanti.
L’asse di Ascensione Retta
La prestanza della montatura non va mai associata prettamente al diametro degli assi, in quanto ci sono altri elementi da prendere in considerazione. Non ha senso avere assi di 100 mm di diametro se poi, per contenere i pesi, il dimensionamento delle parti strutturali viene realizzato con lamierati in alluminio di qualche millimetro di spessore. Non ha senso acquistare una tipologia di cuscinetti realizzati con un alto grado di precisione se poi, per negligenza, non viene rispettata la posizione degli stessi sull’asse.
I cuscinetti vengono realizzati con diverse tipologie di esecuzione e con un proprio grado di precisione. Molti prodotti di basso costo presentano un’eccessiva dispersione dei valori delle dimensioni e del precarico che causano insidiose vibrazioni, cosa che rende difficile prevederne le effettive prestazioni in una data applicazione.
L’elevata capacità di precarico di un cuscinetto evita cedimenti prematuri e consente di tenere sotto controllo le impostazioni iniziali del precarico. Ogni applicazione ha proprie esigenze che impegnano in modo diverso le caratteristiche dei cuscinetti e di conseguenza, per certe applicazioni, le vibrazioni indotte da sfere, rulli e anelli, sono importanti criteri di scelta.
Il corpo dell’asse orario, in acciaio C40, è stato realizzato dal pieno. L’albero, sempre in acciaio C40, ha un diametro di 60 mm e il suo movimento è affidato a due cuscinetti radiali a rulli conici a una corona SKF della serie Explorer, con esecuzione CL7C–60 X 125 X 37 mm.
Questi cuscinetti sono realizzati con una tolleranza ristretta di planarità-concentricità del 50% rispetto ai cuscinetti standard, non richiedono il rodaggio, e sono capaci di formare sin dall’inizio un film lubrificante elastoidrodinamico dei contatti rulli-orletti. Per questo motivo la coppia d’attrito è molto bassa. L’esecuzione CL7C si usa normalmente per ottenere un’elevata rigidezza nei sistemi cuscinetti-ingranaggio, cosa permessa dalle eccezionali capacità di precarico e dalla bassa dispersione dei valori di quest’ultimo.
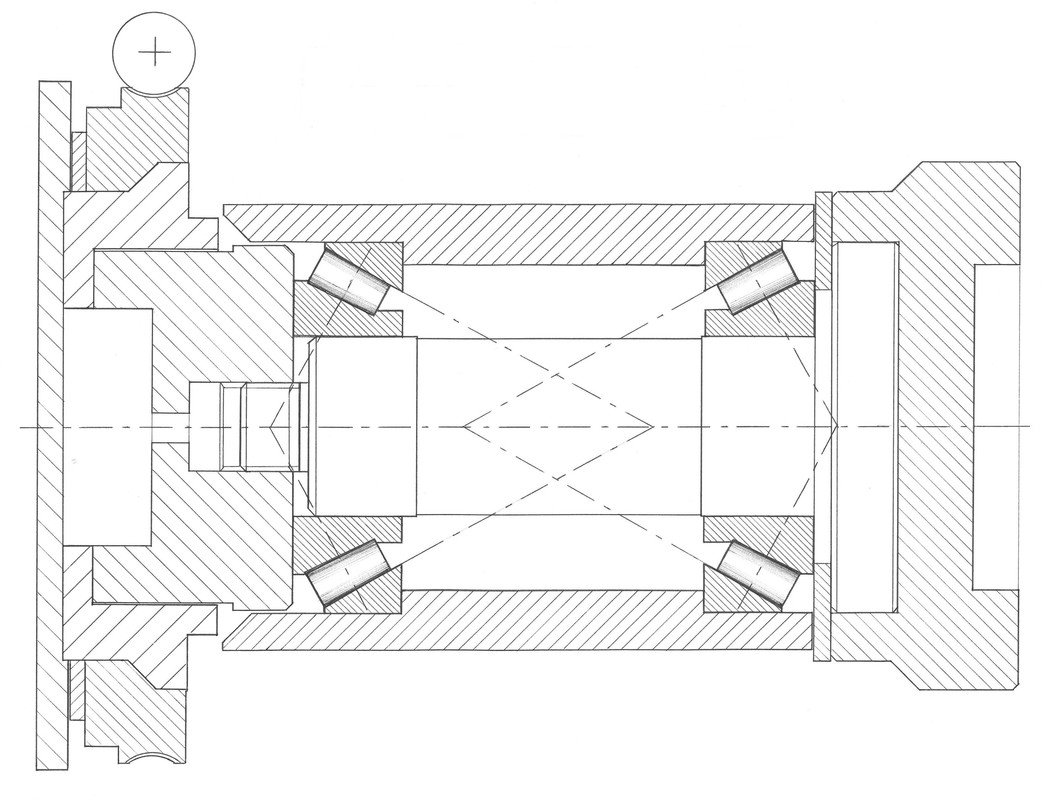
Asse di Ascensione Retta in sezione
I cuscinetti sono accoppiati con disposizione ad <O> (linee di carico che divergono) con i vertici del cono di rotolamento (punti di intersezione) che si sovrappongono. Con questa disposizione il gioco assiale si riduce e i cuscinetti possono sopportare momenti di ribaltamento più elevati. Il precarico avviene per mezzo di una flangia di riscontro frontale con accoppiamento filettato M30 X 1,5.
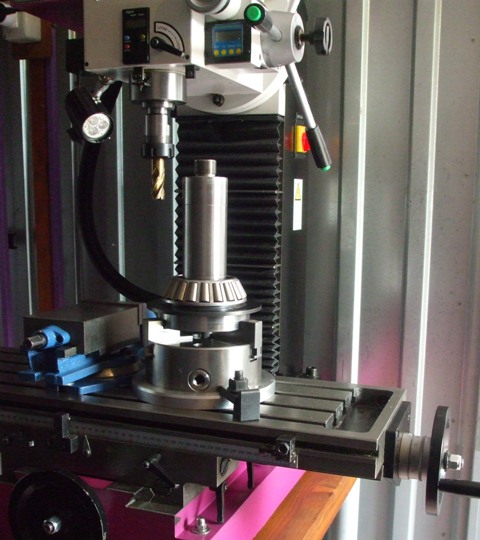
Per facilitare il montaggio dei cuscinetti sull’albero dell’asse orario ho utilizzato un mandrino autocentrante
La corona dentata e la vite senza fine in ascensione retta sono state realizzate dalla ditta Bellincioni. La corona dentata, in Bronzo B14, ha un diametro primitivo di 225 mm, uno spessore totale di 34 mm, e sviluppa 300 denti con un modulo della dentatura pari a 0,75.
La corona dentata ruota su una flangia di interfacciamento basculante, con accoppiamento in tolleranza H7/h6, che svolge il compito di blocco - movimento per mezzo di viti M8 in acciaio inox. Durante l’osservazione, la corona dentata viene bloccata tramite una frizione precaricata a riscontro frontale.
La vite senza fine, in acciaio inox rettificato, ha un diametro primitivo della vite di 28 mm ed è movimentata su cuscinetti a sfera. La tolleranza di lavorazione, verificata con un comparatore universale a quadrante, è risultata di un centesimo di millimetro.
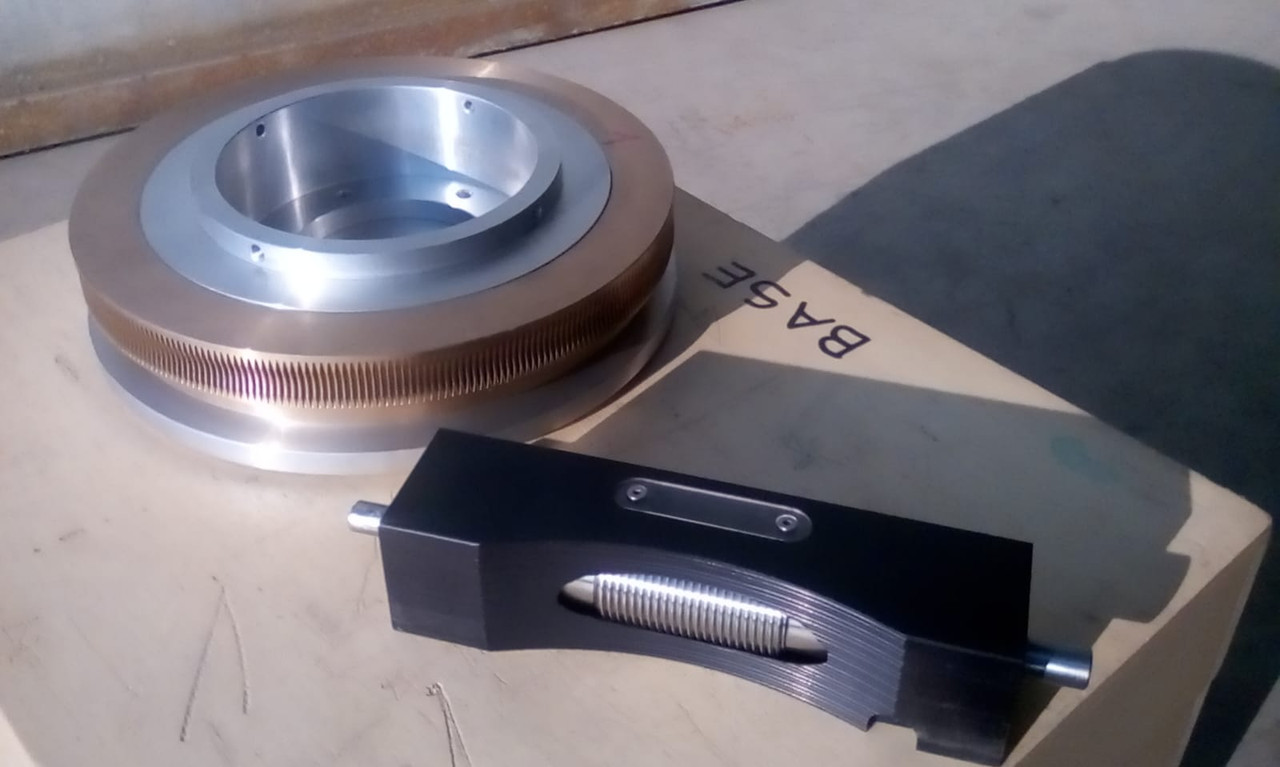
La corona dentata inserita sulla flangia di interfacciamento basculante e la vite senza fine con supporto
Ma perché è opportuno rendere basculante il supporto della corona dentata? Poiché i componenti che formano la montatura equatoriale sono stati realizzati alle macchine utensili con un proprio grado di precisione, che gli viene assegnato in sede di progetto e da questo grado di precisione dipende il campo di tolleranza della lavorazione, ne consegue che il grado di tolleranza risultante sarà dato dalla somma di tutti gli scostamenti generati nella lavorazione.
A fronte di questo, la flangia di interfacciamento basculante mi permette di conseguire la concentricità e la ortogonalità della corona dentata rispetto alla vite senza fine. Per agevolare le operazioni di allineamento, il sistema di riduzione corona dentata – vite senza fine è stato posizionato nella parte posteriore dell’asse orario.
Il grado di tolleranza risultante
Nella lavorazione alle macchine utensili il pezzo da realizzare viene ripreso due o più volte. Se viene utilizzato un mandrino autocentrante, (che è formato da una piattaforma con 3 o 4 guide lungo le quali scorrono le ganasce) la ripresa del pezzo porta sempre a un errore di riposizionamento, in quanto i mandrini autocentranti, anche se realizzati con doppia guida, sono imprecisi per costruzione. Infatti, per serrare le griffe agisci sui pignoni che fanno ruotare la spirale, e a sua volta la spirale ingrana nelle griffe e ne permette lo spostamento. Pertanto, il sistema spirale – griffe, durante il serraggio, si sposta lateralmente.
Supponiamo, ad esempio, di realizzare al tornio parallelo l’albero dell’asse orario con un mandrino autocentrante. Terminata la lavorazione da un lato si deve rimuovere il pezzo per continuare la lavorazione sul lato opposto. Il pezzo viene quindi fissato sul mandrino autocentrante che, grazie all’azione di serraggio simmetrica dei suoi componenti, attesta il pezzo sull’asse principale di rotazione con uno scostamento, delle tolleranze di forma e di posizione delle superfici d’appoggio dei cuscinetti (circolarità – parallelismo – planarità dello spallamento), evidenziato nell’ordine di 2 – 5centesimi di millimetro.
Il mio tornio ha un mandrino autocentrante di 200 mm di diametro della BISON-BIAL di ottima fattura eppure, se appoggio il tastatore del comparatore sulla superficie del pezzo per continuare la lavorazione sul lato opposto, si rilevano scostamenti di 2 – 3 centesimi di millimetro. Ne consegue, che se il pezzo non viene centrato nella fase di serraggio sul mandrino, ad ogni riposizionamento dello stesso, si generano scostamenti compresi fra i 2 – 3 centesimi di millimetro. A questo punto, quale potrebbe essere il grado di tolleranza risultante?
Con il mio mandrino autocentrante riesco a contenere lo scostamento nell’ordine di un centesimo di millimetro, utilizzando (con pazienza e meticolosità) una mazzuola di gomma e un comparatore universale. Con questo accorgimento l’albero dell’asse orario è stato realizzato con un grado di precisione nell’ordine di un centesimo di millimetro.
Da tenere in considerazione, che sebbene i cuscinetti a rulli conici SKF della serie Explorer siano assemblati con una tolleranza molto stretta e un precarico molto spinto, presentano comunque un gioco di esercizio di piccola entità, ma pur sempre un gioco che genera uno scostamento.
Se cerchiamo la massima precisione, come prima cosa dovremmo dimenticarci delle piattaforme autocentranti, e lavorare prettamente con piattaforme a 4 griffe indipendenti. Con queste ultime si deve procedere con operazioni di aggiustaggio.
Queste operazioni comunque necessitano di tempi lunghi e di manodopera specializzata che, per coloro che devono rivolgersi a un’officina, andranno inevitabilmente a incidere sui costi. La precisione quindi non dipende esclusivamente dalle macchine utensili utilizzate, (questo vale anche per le macchine utensili a controllo numerico) ma dipende soprattutto dalla meticolosità dell’operatore.
Conseguire la concentricità e l’ortogonalità della corona dentata
Per conseguire la concentricità della corona dentata ho utilizzato un comparatore universale a quadrante con supporto magnetico ed ho eseguito, in ordine cronologico, le seguenti operazioni:
- Ho posizionato il comparatore sopra il corpo dell’asse orario.
- Poi, ho appoggiato il tastatore sulla flangia di interfacciamento basculante in un punto prestabilito e ho azzerato l’indice del comparatore.
- A questo punto, ho iniziato a ruotare a mano l’asse orario osservando contemporaneamente lo scostamento dell’indice del comparatore.
- L’indice del comparatore ha iniziato a muoversi in una direzione fino a 180° e nella direzione opposta da 180 a 360°.
- Con le viti di aggiustaggio della flangia di interfacciamento basculante ho azzerato lo scostamento evidenziato dal comparatore, e conseguito
la concentricità della stessa.
- A questo punto, si deve verificare l’ortogonalità della flangia di interfacciamento basculante. Per questo, ho posizionato il tastatore sullo spallamento della stessa e con le viti di aggiustaggio ho azzerato lo scostamento evidenziato dal comparatore.
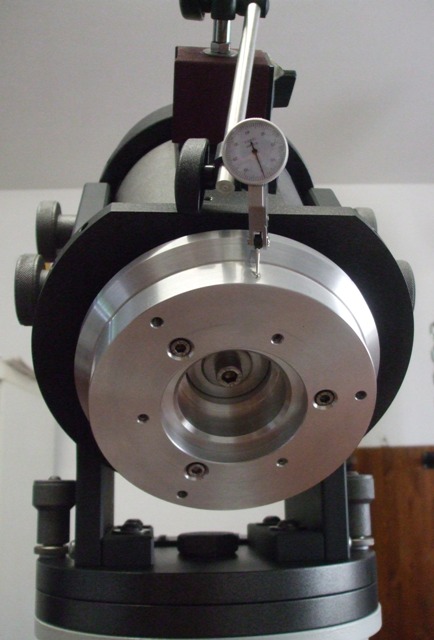
Il tastatore del comparatore è posizionato sulla flangia di interfacciamento basculante della corona dentata
Conseguito l’ortogonalità, è necessario ricontrollare la concentricità. Queste operazioni vengono eseguite in successione, fino a conseguire, con una buona dose di pazienza, la concentricità e l’ortogonalità della flangia di interfacciamento basculante.
Questa verifica può eseguita da chiunque sia possessore di una montatura equatoriale alla tedesca, magari nell’occasione di una manutenzione o revisione della stessa. In questo caso, si deve rimuovere la corona dentata dalla sua sede e posizionare un comparatore sul corpo della montatura con il tastatore appoggiato sulla sede della corona dentata (non serve utilizzare un comparatore professionale, si può acquistarlo con soli 40 euro completo di supporto magnetico).
Se il corpo dell’asse orario è stato realizzato in alluminio, la base magnetica del supporto del comparatore non fa presa sul corpo stesso, ed è pertanto necessario posizionare una basetta di interfacciamento metallica fra la base del comparatore e il corpo dell’asse orario.
Verifiche eseguite su alcune montature commerciali hanno evidenziato errori di concentricità di 15 centesimi! In questa circostanza, se andiamo a congiungere la vite senza fine alla corona dentata in un punto prestabilito, che deve essere assolutamente il punto più esterno della circonferenza primitiva dell’ingranaggio rispetto all’asse di progetto, si avrebbe un accoppiamento senza gioco meccanico in questo punto, mentre ad una rotazione di 180° si avrebbe il gioco meccanico assoluto.
La trasmissione del moto nell’accoppiamento corona dentata – vite senza fine
Nella trasmissione del moto il gioco meccanico è uno spazio di movimento non trasmesso durante l’inversione di direzione, ed è determinato dallo spazio tra i denti dell’accoppiamento corona dentata – vite senza fine. A causa dell’esistenza di tale spazio, durante l’inversione di moto della vite senza fine la corona dentata rimarrà ferma fino a quando i denti della vite senza fine e della corona dentata torneranno ad essere in contatto.
Per resettare il gioco meccanico tra la corona dentata e la vite senza fine, alcuni costruttori integrano il supporto della vite senza fine con un elemento di posizionamento a molla, il quale esercita una pressione costante sulla corona dentata, eliminando così ogni possibile gioco generato dall’eccentricità insita nel montaggio della stessa. In questo caso, il gioco meccanico viene resettato, ma non si risolve il problema della perpendicolarità, poiché la corona dentata potrebbe non essere ortogonale con la vite senza fine.
Altri invece, eseguono una rodatura della vite senza fine sulla corona dentata. Questa soluzione però, se eseguita con livelli di pressioni elevate, potrebbe generare una usura per adesione dell’ingranaggio (in genere il rodaggio e la lucidatura vengono considerate come usura normale). Per tale motivo i materiali utilizzati sono acciaio su bronzo.
L’usura adesiva, che nella forma più grave porta al grippaggio, è possibile anche quando la lubrificazione è insufficiente o inadeguata. Pertanto, se una rodatura viene eseguita su un accoppiamento corona dentata – vite senza fine assemblato con un disallineamento meccanico, si possono raggiungere localmente livelli di pressione tali da deformare plasticamente il materiale con possibile danneggiamento della corona stessa.
Accoppiamento corona dentata – vite senza fine
La frizione della corona dentata è precaricata tramite quattro pressori a puntale e molla con terminale in polimero. Il precarico mi permette di ruotare manualmente l’asse orario. Durante l’osservazione degli oggetti celesti la frizione viene bloccata, con riscontro frontale, tramite due volantini M8 con perno filettato in ottone. L’accostamento della vite senza fine alla corona dentata avviene per mezzo di un congegno meccanico realizzato in alluminio Anticorodal 6082, costituito da un componente statico accoppiato a un componente mobile.
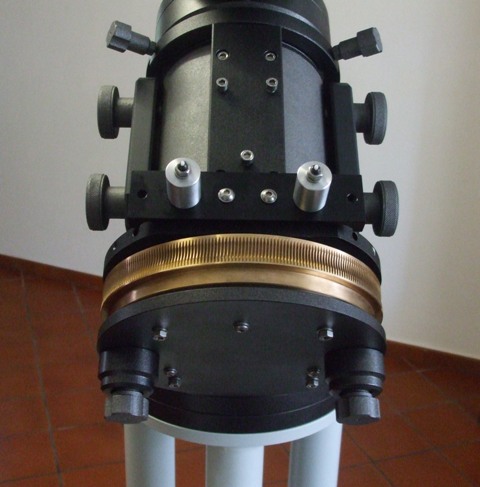
La corona dentata dell’asse orario. Si notino i quattro pressori a molla sulla flangia di riscontro, i due volantini di blocco e il componente statico integrato dei due pistoncini e i pressori a puntale
Il componente statico è formato da un profilo piatto integrato con due pistoncini di 24 mm di diametro, realizzati in tolleranza g6. Nella parte superiore dei due pistoncini sono avvicendati due pressori a puntale e molla con terminale in polimero. Il componente statico viene posizionato e fissato in modo permanente nella parte superiore del corpo dell’asse orario, rispettando le quote di progetto.
Il componente mobile invece fa parte integrale con il supporto della vite senza fine, ed è formato da un profilo piatto avvicendato con due cilindri con foro centrale di 24 mm di diametro, realizzati in tolleranza H7. Le due sezioni del congegno meccanico vengono infine unite tramite l’accoppiamento cilindro – pistone.
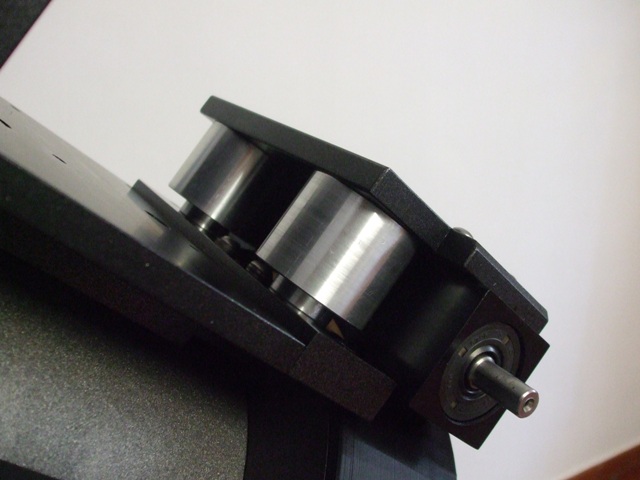
Il componente mobile del congegno meccanico, integrato con la vite senza fine, è accoppiato al componente fisso
Sul componente statico sono stati inseriti due montanti che hanno la funzione di sostenere una basetta realizzata da un profilo piatto in alluminio Anticorodal 6082. Sulla basetta sono avvicendati due pressori a puntale e molla con terminale in polimero.
Questi ultimi sono contrapposti ai due pressori posizionati sul componente statico (che invece spingono per discordare) e hanno la funzione esercitare una pressione costante della vite senza fine sulla corona dentata. L’accostamento della vite senza fine alla corona dentata viene quindi conseguito con precarico meccanico per mezzo dei quattro pressori.
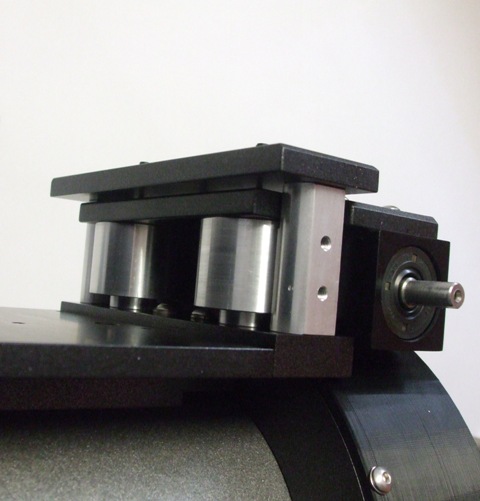
La basetta è posizionata, tramite i due montanti, sopra il componente mobile del congegno meccanico.
L’accoppiamento cilindro – pistone del congegno meccanico mi permette di rimuovere in pochi minuti la vite senza fine, ad esempio per una ispezione o manutenzione della stessa e della corona dentata. Per ripristinare l’accostamento della vite senza fine alla corona dentata occorre semplicemente procedere con le operazioni di aggiustaggio del precarico dei pressori a puntale e molla.
Il sistema di puntamento Astro Electronic FS2
Il sistema di puntamento Astro Electronic FS2 a 30V è costituito da una centralina dove sono visibili da una parte i connettori per la pulsantiera,per l’autoguida a 15 pin (tipo ST4), porta autoguida 6 pin, porta encorder e porta RS - 232, e dall’altra parte i connettori per i motori AR e DEC, fusibile e il cavo di alimentazione.
Il motore in ascensione retta, fornito insieme al sistema di puntamento FS 2, è un SECM5 con riduzione ad ingranaggi 1:16. Il motore è stato posizionato all’interno di un involucro a forma di parallelepipedo realizzato con profili di piatto di alluminio Anticorodal 6082 di vario spessore.
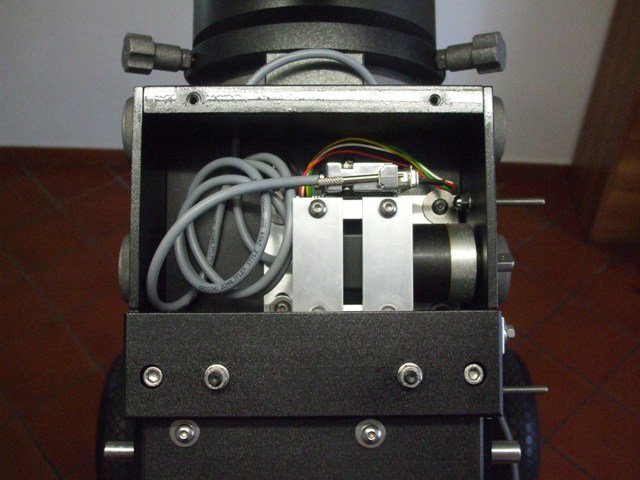
Il motore, inserito all’interno dell’involucro, viene tenuto in posizione tramite una basetta collegata alla base.
La trasmissione del moto avviene per mezzo di due pulegge sincrone tipo GT2 - 36 denti e una cinghia chiusa GT2 in Neoprene di 6 mm di larghezza con sviluppo di 280 mm. La cinghia viene mantenuta in tensione tramite un cuscinetto di rinvio posizionato su una basetta basculante.
Il sistema di trasmissione del moto è protetto da un carter che viene bloccato in posizione tramite due volantini con madrevite M5, molto pratici da rimuovere nel caso sia necessario una veloce ispezione dello stato della cinghia di trasmissione.
I componenti meccanici posizionati all’interno dell’involucro non sono stati anodizzati, poiché essendo non visibili dall’esterno, ho ritenuto non necessario eseguire l’operazione.
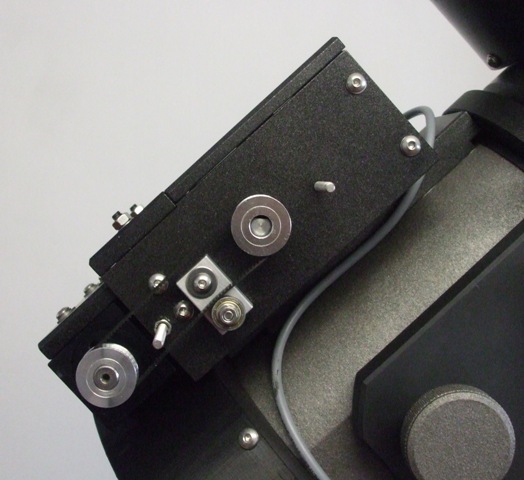
Il sistema di trasmissione del moto
Asse di Declinazione
Il corpo dell’asse orario viene congiunto al corpo dell’asse di declinazione per mezzo di due flange a riscontro frontale realizzate in alluminio Anticorodal 6082. Hanno rispettivamente un diametro di 178mm e sono accorpate tramite di un accoppiamento foro – albero in tolleranza H7/g6.
Il corpo dell’asse di declinazione, in alluminio Anticorodal 6082, è stato realizzato dal pieno. L’albero, in acciaio C40, ha un diametro di 45 mm e il suo movimento è affidato a due cuscinetti radiali a rulli conici a una corona SKF della serie Explorer, con esecuzione CL7C – 45 X 95 X 29 mm. I cuscinetti sono accoppiati con disposizione ad <O>,con i vertici del cono di rotolamento che si sovrappongono, e sono precaricati tramite una flangia di riscontro frontale con accoppiamento filettato M30 X 1,5.
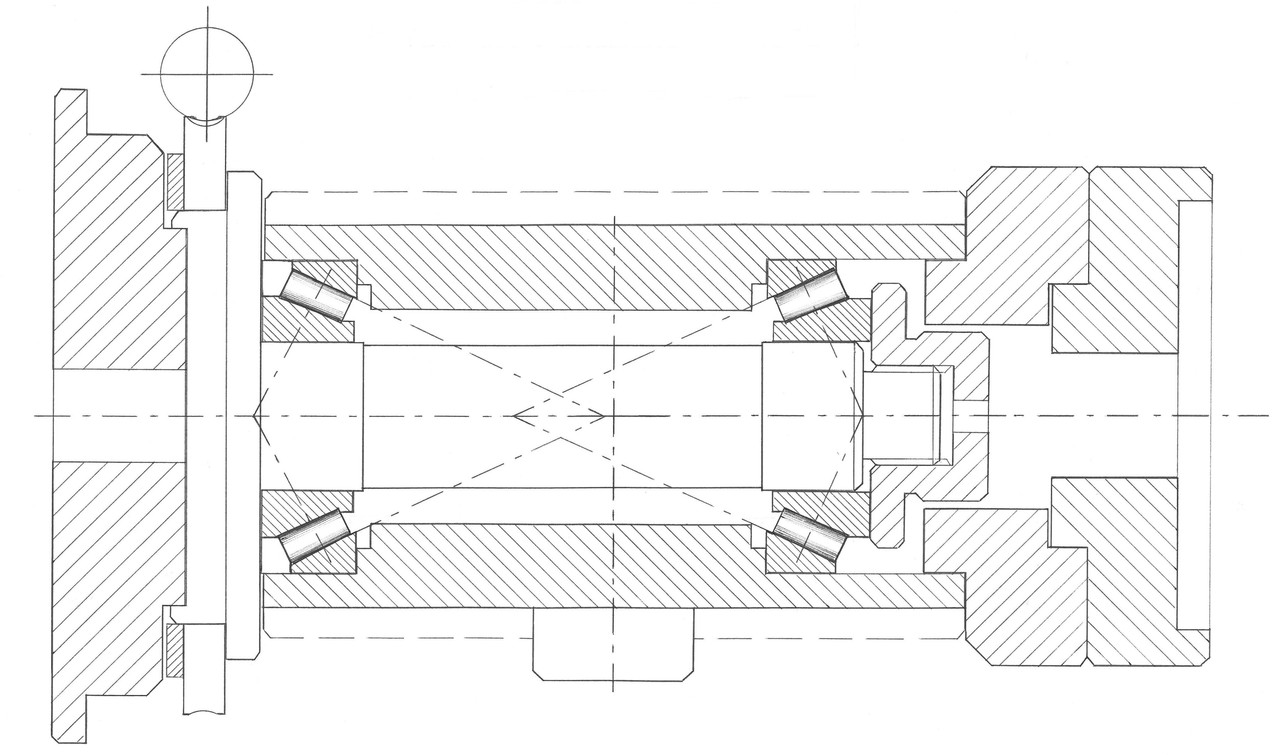
Asse di Declinazione in sezione
La corona dentata in declinazione, in Bronzo B14, ha un diametro primitivo di 180 mm, uno spessore totale di 13 mm e sviluppa 240 denti con modulo della dentatura pari a 0,75. La corona dentata ruota su una flangia di interfacciamento con accoppiamento H7/h6, ed è precaricata tramite una frizione a riscontro frontale che mi permette di ruotare manualmente l’asse in declinazione. Durante l’osservazione degli oggetti celesti, la frizione viene bloccata, con riscontro frontale, per mezzo di due volantini M8 con perno filettato in ottone.
La vite senza fine, in acciaio inox, ha un diametro primitivo di 28 mm ed è movimentata su cuscinetti a sfera. L’accoppiamento corona dentata – vite senza fine e i componenti per la trasmissione del moto sono stati assemblati con lo stesso procedimento utilizzato per l’asse orario.
Il blocco degli assi
Per il trasporto dello strumento, dal punto di giacenza al punto di osservazione, l’asse orario viene bloccato tramite tre volantini posizionati a 120°, mentre l’asse di declinazione viene bloccato per mezzo di due volantini contrapposti.
In questo modo non è necessario bloccare le frizioni delle due corone dentate, e le sollecitazioni, che si potrebbero generare da un trasporto dello strumento effettuato su un piano calpestabile non omogeneo, non si riflettono sull’accoppiamento corona dentata – vite senza fine, che rimane in precarico e libero di muoversi.
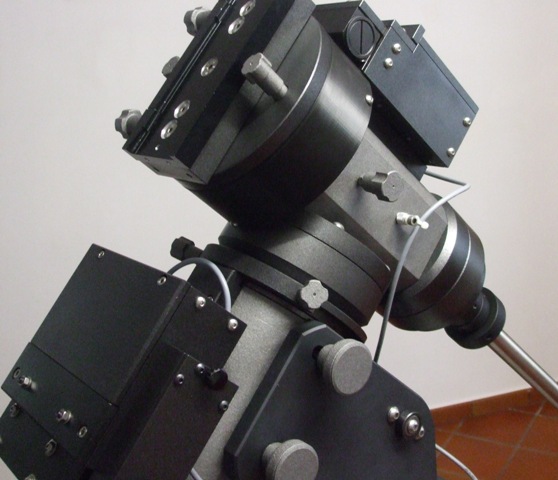
I volantini di blocco asse AR/DEC. Si notino due dei tre volantini di blocco dell’asse orario e uno dei due volantini di blocco dell’asse di declinazione
Il blocco degli assi con un sistema meccanico totalmente indipendente dall’accoppiamento corona dentata – vite senza fine presenta però un’insidia, alla quale bisogna prestare attenzione. Prima di iniziare l’osservazione si devono allentare i volantini di blocco degli assi. Il rischio è di avviare la motorizzazione con gli assi bloccati, sarebbe un disastro. Nella versione precedente gli assi venivano bloccati tramite un braccio meccanico, più percettibile del volantino, ma che esteticamente era sgradevole da vedere.
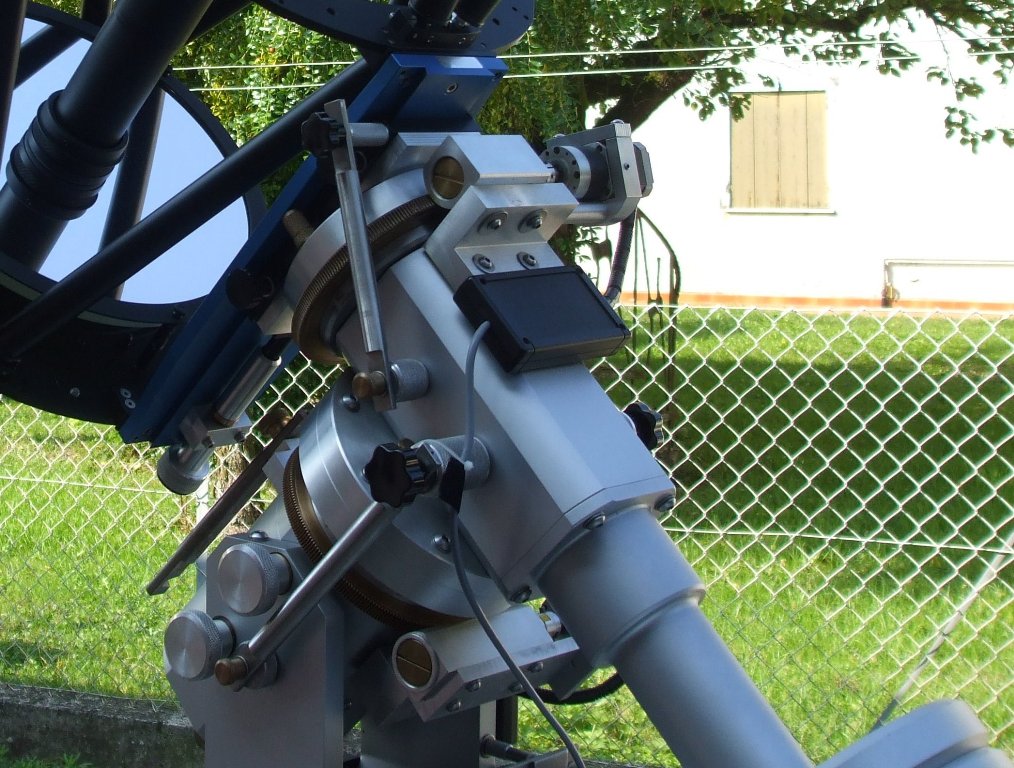
La versione originale della montatura prevedeva il blocco degli assi con un braccio meccanico
Bilanciare gli assi
Per bilanciare il tubo ottico in ascensione retta, la montatura è provvista di quattro contrappesi autocostruiti, di cui tre in posizione stabile e uno mobile. L’asta contrappesi, realizzata in acciaio inox 304 dal pieno, ha un diametro di 30 mm e presenta una lunghezza complessiva di 470 mm.
I tre contrappesi stabili, realizzati in Fe 510 e verniciati nero a polvere, hanno un peso di 10 chilogrammi cadauno, per un totale di 30 chilogrammi. I contrappesi vengono fermati in posizione tramite una ghiera.
Il contrappeso mobile, realizzato in acciaio C 40 e verniciato nero a polvere, ha un peso di 14 chilogrammi ed è il contrappeso che viene utilizzato per bilanciare il tubo ottico in ascensione retta durante le osservazioni. In totale, la montatura ha un montare di contrappesi di 44 chilogrammi.
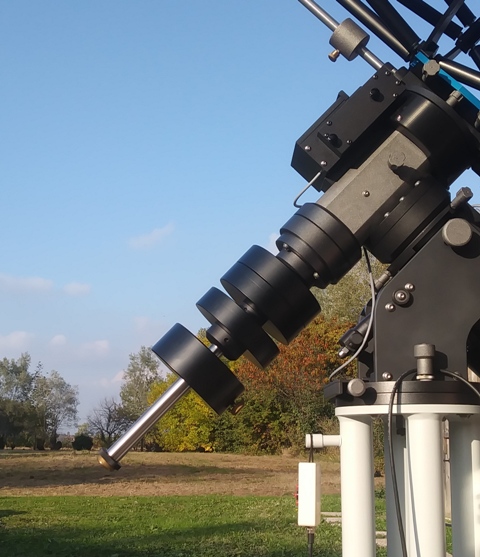
La posizione dei contrappesi con il tubo ottico senza accessori bilanciato in ascensione retta
Come si può notare dalla foto i contrappesi stabili sono posizionati il più vicino possibile al fulcro del corpo dell’asse in ascensione retta. Questa disposizione non è casuale. Infatti, quando si hanno dei corpi in rotazione attorno a degli assi, si deve tenere in considerazione la distanza di tali masse dall’asse di rotazione.
Ne consegue, che posizionare un carico eccessivo all’estremità dell’asta contrappesi, si esercita un carico assiale di punta che può creare un movimento flettente sulla stessa. Per quanto sia paradossale, è meglio avere 20 chilogrammi il cui il centro di massa è posizionato a 30 centimetri, che averne 10 il cui centro di massa è posizionato a 50 centimetri.
A dimostrazione di ciò, per i primi due anni (come riportato all’inizio della recensione) ho utilizzato il Dall Kirkham 310/6000 (peso complessivo di 34 Kg) sulla montatura autocostruita del rifrattore apocromatico, che aveva una testa equatoriale di 35 chilogrammi di peso al netto dei contrappesi.
Per non zavorrare eccessivamente la montatura, ho realizzato un’asta contrappesi di notevole lunghezza e posizionato tutti i contrappesi, per un totale di 24 chilogrammi, all’estremità della stessa. Come si può notare dalla foto, questa disposizione oltre ad essere deleteria è anche esteticamente sgradevole da vedere.
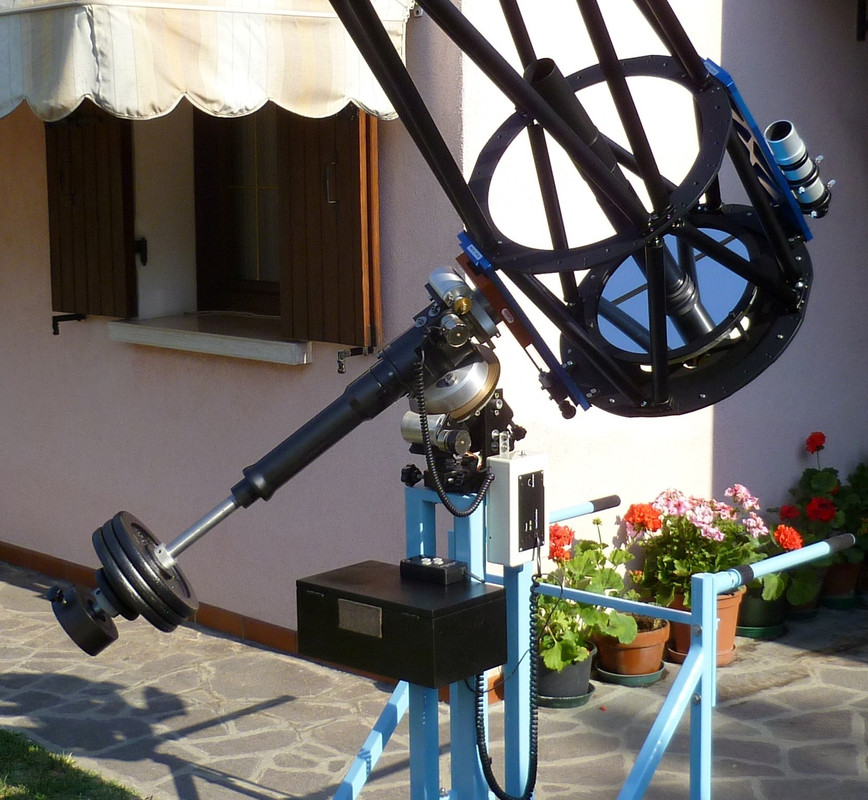
La montatura equatoriale autocostruita del rifrattore apocromatico. Si notino i contrappesi posizionati all’estremità dell’asta
Per bilanciare il tubo ottico in declinazione viene utilizzato un contrappeso autocostruito avvicendato ad un congegno meccanico a traslazione. Il contrappeso di 1,2 chilogrammi, realizzato in Fe 510, è inserito su un’asta in alluminio Anticorodal 6082 con diametro di 19 mm e 400 mm di lunghezza, posizionata di fronte alla slitta Losmandy.
Il congegno meccanico a traslazione, collocato tra la slitta Losmandy e il morsetto, trasforma il moto rotatorio mediante vite conduttrice in un movimento lineare. Il moto viene conseguito per mezzo di un accoppiamento vite – madre vite, integrato con due cuscinetti assiali a sfera SKF BA8 contrapposti fra loro e precaricati.
Il movimento lineare dell’accoppiamento vite – madre vite mi permette di spostare il tubo ottico in declinazione di pochi millimetri e conseguire così il giusto equilibrio dello stesso in tutta sicurezza, poiché viene neutralizzato ogni qualsiasi slittamento improvviso della slitta Losmandy dal morsetto.
Fino a poco tempo fa, utilizzavo regolarmente questo congegno per bilanciare in declinazione il Dall Kirkham durante le osservazioni. Per agevolare il movimento della slitta Losmandy sul morsetto, il bilanciamento del tubo ottico doveva essere eseguito con la montatura in posizione di riposo, ossia quando la barra dei contrappesi è rivolta verso il basso (in questo modo lo scorrimento della slitta Losmandy sul morsetto veniva conseguito per mezzo delle due superfici piatte).
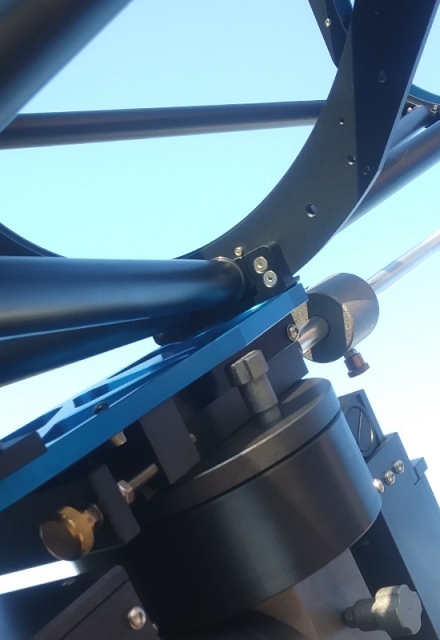
Il congegno meccanico che mi consente di bilanciare il tubo ottico in declinazione.
Adesso il tubo ottico viene bilanciato in declinazione utilizzando il congegno meccanico a traslazione e il contrappeso di 1,2 chilogrammi. L’operazione è suddivisa in due fasi:
1) il tubo ottico viene bilanciato senza accessori per mezzo del congegno meccanico a traslazione. In questa circostanza il contrappeso di 1,2 chilogrammi viene posizionato il più vicino possibile alla slitta Losmandy. Questa condizione viene utilizzata con il telescopio a riposo e durante il trasporto su ruote.
2) durante l’osservazione, per controbilanciare il peso degli accessori utilizzati (diagonali, torretta binoculare, oculari,fotocamere), il contrappeso di 1,2 chilogrammi viene spostato verso l’esterno.
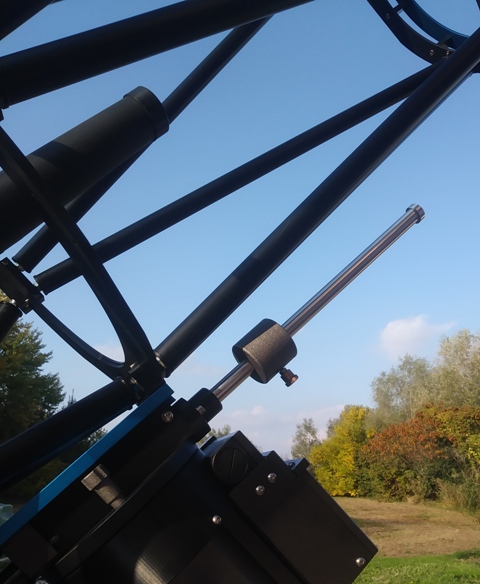
Il contrappeso di 1,2 chilogrammi che mi consente di bilanciare il tubo ottico in declinazione durante le osservazioni.
Due importanti riflessioni
Per concludere, vorrei rivolgere all’attenzione degli astrofili due riflessioni. Assistiamo oggi la proposta di nuove montature equatoriali di provenienza orientale integrate con elettroniche sempre più evolute che, a detta dei costruttori, sono in grado di sostenere in modo accettabile strumenti di diametro generoso.
Queste montature presentano caratteristiche e qualità molto variabili. Sono disponibili versioni motorizzate con computer, dalle piccole alle ammiraglie, con portata dichiarata fino a 50 chilogrammi e con costi abbastanza contenuti.
La mia EQ 8, che sostiene il rifrattore apocromatico 145/1500, è accreditata di un carico massimo utile di circa 50 chilogrammi eppure, dopo una focheggiatura, osservando in visuale a 320 ingrandimenti (oculare Explore Scentific 4,7mm), le vibrazioni sono annullate in circa 2 – 3 secondi.
Con ciò non voglio screditare la mia EQ8, anche perché molto probabilmente nella classe dei 40 – 50 chilogrammi di portata dichiarata, salvo forse le montature di classe superiore (e costo relativo), nessuna montatura commerciale sarebbe in grado di sostenere adeguatamente uno strumento di 35 chilogrammi di peso e 180 centimetri di lunghezza.
Con questo, non sto affermando che le montature si deformano con il peso dei tubi ottici, ci mancherebbe altro. Del resto, basti pensare che l’albero dell’asse orario di una montatura equatoriale di 40 mm di diametro in metallo pieno che ruota su cuscinetti, è paragonabile all’asse di una ruota d’automobile destinata a ben altri carichi!
Al contrario di quanto si pensi, il <tallone d’Achille> di una montatura equatoriale alla tedesca è in primo luogo insito nel collegamento tra le flange di interfacciamento (o base della montatura) che mi consentono la regolazione in azimut, e in secondo luogo, è insito nell’interfacciamento dell’asse di declinazione al tubo ottico.
Da non sottovalutare anche il comportamento della montatura nelle diverse posizioni assunte dal tubo ottico con gli accessori, perché se si cambia anche un solo oculare e se ne mette uno di peso diverso, la posizione del baricentro si modifica, e se il tubo ottico non viene poi bilanciato, si rischia di compromettere la stabilità. Quanti di voi bilanciano il tubo ottico ogni qualvolta si cambiano gli accessori?
Un'altra questione è come viene distribuito il peso dello strumento sulla montatura. Un conto è avere uno Schimdt Cassegrain C11 (610 mm di lunghezza X 12 Kg di peso), un altro avere un rifrattore Istar FrT da 127 mm a F12 (1580 mm di lunghezza X 9,8 Kg di peso). Per assurdo, con una stessa ipotetica montatura (ad esempio una EQ6) il tempo di smorzamento delle vibrazioni sarà minore con lo Schimdt Cassegrain, sebbene quest’ultimo sia più pesante del rifrattore, in quanto la distanza dall’asse di rotazione (o momento d’inerzia) è minore e più vicino al fulcro di equilibrio.
Ad oggi, le montature equatoriali vengono pubblicizzate dai costruttori come montature leggere e allo stesso tempo molto robuste, in grado di sostenere un telescopio che ha un peso pari al doppio della testa equatoriale. A dimostrazione di questo, prendiamo come riferimento una montatura equatoriale di provenienza orientale. Il costruttore dichiara che <il progetto accurato, consente di contenere il peso della testa equatoriale a soli 15 chilogrammi per una portata di 35 chilogrammi>. Ciò nonostante i buoni presupposti del costruttore, sarebbe interessante verificare i tempi di smorzamento delle vibrazioni della montatura in oggetto con il mio rifrattore apocromatico.
C’è una teoria che riguarda il percorso delle linee di forza che percorrono i materiali sollecitati. In pratica, la direzione di queste linee di forza dovrebbe essere senza zone di strozzatura, altrimenti si avrebbero sollecitazioni anormali. Al riguardo, anche le parti strutturali della montatura se realizzate per fusione, e per giunta con spessori ristretti, non garantiscono una sufficiente gradualità nello scaricare sul treppiede, o sulla colonna, le sollecitazioni dei contrappesi e del tubo ottico.
Da qui, se ne deduce che una montatura equatoriale, cui i componenti meccanici sono stati realizzati dal pieno alle macchine utensili, dovrebbe garantire una maggiore stabilità. Altresì, è fondamentale che le flange di interfacciamento alla base della montatura siano di diametro generoso, e che la massa del corpo dell’asse orario sia almeno il doppio della massa del corpo dell’asse in declinazione. In questo contesto, la qualità dei materiali utilizzati per la realizzazione dei vari componenti e il grado precisione meccanica, sono comunque imprescindibili. Ragione per cui, ha maggiore importanza prendere come riferimento la massa della testa equatoriale e non la portata dichiarata, in quanto i costruttori non utilizzano un metodo standard di riferimento e non dichiarano a quale distanza del centro di massa del carico, rispetto alla piastra di attacco del tubo ottico, hanno valutato tale carico limite.
Per farvi un esempio, si trovano in commercio montature con testa equatoriale di 70 chilogrammi di peso, con portata dichiarata di 120 chilogrammi, e montature con testa equatoriale di 120 chilogrammi di peso, con portata dichiarata di 110 chilogrammi. Vi sembra logico?
A fronte di questo, vi invito a osservare nella foto seguente la differenza di dimensioni fra la mia EQ 8, che ha una testa equatoriale di 25 chilogrammi di peso, e la montatura autocostruita, che ha una testa equatoriale di 85 chilogrammi di peso.
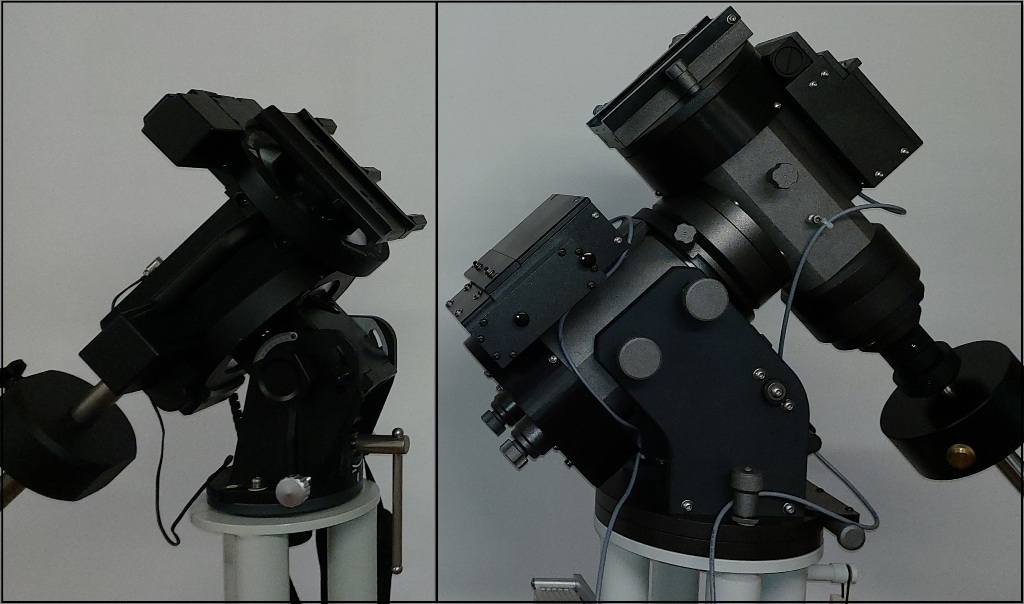
La EQ8 e la montatura autocostruita a confronto
La base della montatura autocostruita (flange di interfacciamento in azimut e asse in ascensione retta) è imponente, se comparata alla base della EQ 8, mentre il corpo dell’asse di declinazione della medesima, che a prima vista sembrerebbe di uguale dimensioni di quella autocostruita, è in realtà cavo all’interno per contenere l’elettronica. Le notevoli dimensioni delle flange di interfacciamento in azimut (274 mm) e la massa del corpo dell’asse orario (50 Kg) della montatura autocostruita, assicurano una maggiore stabilità e smorzamento delle vibrazioni.
Per confronto, dopo una focheggiatura, osservando in visuale a 320 ingrandimenti con il rifrattore apocromatico, le vibrazioni scompaiono immediatamente appena allontano la presa dalla manopola della messa a fuoco (con la EQ 8 invece le vibrazioni sono smorzate in circa 2 – 3 secondi).
Tengo a precisare comunque che il test dello smorzamento delle vibrazioni dopo la focheggiatura o attestando un colpetto al tubo ottico non è sufficientemente idoneo a valutare la stabilità complessiva della montatura, poiché possono essere presenti dei difetti più insidiosi che, pur non disturbando l’osservazione visuale, sono però deleteri in campo fotografico.
La seconda riflessione che vi propongo è la seguente: costruire oggi una montatura equatoriale in proprio è un risparmio? Dipende!
Dipende soprattutto dalla configurazione e dalle dimensioni del tubo ottico cui disponiamo. Se abbiamo uno strumento di piccola – media apertura e di lunghezza contenuta, l’acquisto di una montatura di provenienza orientale è certamente consigliato, poiché il costo del materiale acquistato per realizzare la montatura è superiore al prezzo di una montatura equatoriale commerciale similare.
Diverso invece è il discorso se facciamo riferimento al prezzo di un prodotto similare offerto da ditte del settore per una certa fascia alta di mercato. In questo caso, se abbiamo una officina meccanica propria con macchine utensili e molto tempo a disposizione, il risparmio è consistente.
A dimostrazione di ciò, per l’acquisto del materiale necessario per realizzare la montatura, ho speso circa 6000 euro (è una valutazione approssimativa). Il costo comprende l’acquisto dei materiali utilizzati per la lavorazione alle macchine utensili, le corone dentate e le rispettive viti senza fine, i cuscinetti, la viteria, la motorizzazione e l’anodizzazione.
Nei costi di realizzazione non sono incluse le ore di lavoro svolte per eseguire il progetto completo e dettagliato della montatura (che contrariamente a quanto si pensi sono svariate ore), le ore di lavoro alle macchine utensili e i costi di consumo di energia elettrica.
Individuare una montatura equatoriale di confronto di una certa fascia alta di mercato non è facile. Oltretutto, la comparazione dovrebbe essere eseguita prendendo come riferimento la massa della testa equatoriale (la mia montatura ha una testa equatoriale di 85 chilogrammi), e in questa fascia di mercato si potrebbero prendere in considerazione la GM 3000 HPS, che ha un GoTo con Encorders assoluti sugli assi (peso testa equatoriale 65 Kg, prezzo circa 17000 euro), la Astro-Physics 1600 GTO (peso testa equatoriale 65 Kg, prezzo circa 14000 euro), oppure la FORNAX 150 MC5 (peso testa equatoriale 70 Kg, prezzo circa 11000 euro.
Queste montature, a detta dei costruttori, hanno una progettazione e costruzione meccanica all’avanguardia. Sono fornite con Software di ultima generazione che garantiscono una elevata precisione di allineamento e inseguimento, con prestazioni migliori rispetto al sistema GoTo FS2.
Ciò non toglie comunque che sebbene quest’ultimo sia datato, è di fatto un Software facile da utilizzare e insegue in modo fantastico. Per l’osservazione e la ripresa degli oggetti del sistema solare fornisce un elevato standard di qualità alla pari delle motorizzazioni di ultima generazione.
Il confronto tra i costi di acquisto delle montature citate e i costi di realizzazione della montatura autocostruita è a vantaggio di quest’ultima, poiché le concorrenti hanno un costo maggiore, del doppio o addirittura del triplo (vedi la GM 3000 HPS), a fronte di una massa della testa equatoriale minore.
Ciò nonostante, un autocostruttore può adeguare continuamente la montatura ai propri desideri, e l’acquisto di una motorizzazione GoTo con Software di ultima generazione e con Encorders assoluti in entrambi gli assi potrebbe, in futuro, essere il passo successivo da intraprendere.
Cieli sereni
Roberto